Product costs, also known as cost of goods sold (COGS), are direct material, direct labor, and manufacturing overhead. COGS are typically the highest category of a manufacturing company’s cost, and they have a huge impact on the company’s competitiveness.
COGS are inherently added to products as they are designed and made ready for production. They are inherent because they have been pre-established by the design. The COGS are driven into the product by employees responsible for four key designs that drive COGS:
- The product’s design
- The manufacturing process design
- The manufacturing equipment and tooling design and usage plan
- The value stream / supply chain design
Company employees have differing levels of influence on a product’s inherent COGS. Each of these designs impact COGS. These costs often become part of the standard cost of the product.
The illustration below depicts the company functions that influence product cost, in descending order, based on a weighted value of their influence on direct materials, direct labor, manufacturing overhead and depreciable capital. I’ve included a column for depreciable capital, even though it is often included within manufacturing overhead, because it has a large impact on a company’s cash flow and return on assets.
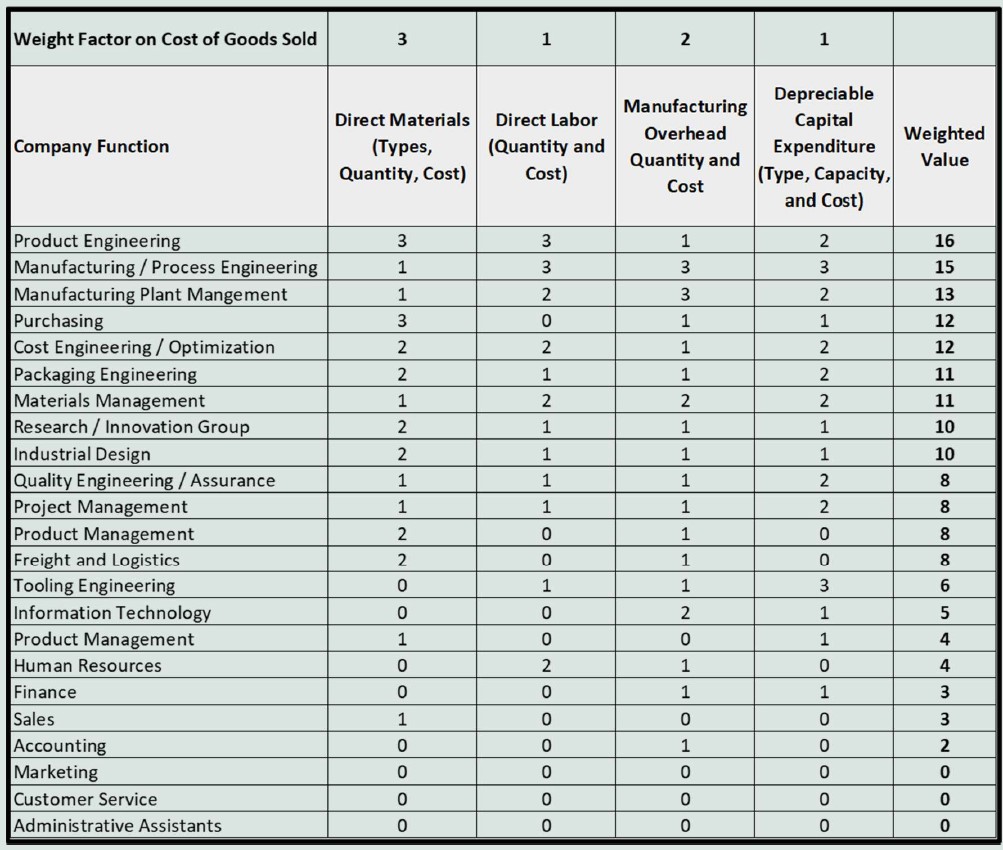
A weighting factor of 1 to 3 is assigned to the four columns based on how much impact each category has on the overall product cost. Direct material has the highest factor of 3. A score of 1 to 3 is also assigned to the company functions’ influence on a column category.
For example, the company function with most influence on product cost is product engineering. They control the product design which directly defines direct materials and indirectly, but significantly defines direct labor, manufacturing overhead and capital.
The next company function with high influence is manufacturing / process engineering. They develop the manufacturing process including the usage of direct labor, manufacturing overhead, and capital.
The main point of the table is to show how much influence the different functions within a company have on the company’s product costs. Then provide a way for the top influencing functions to excel at optimizing product costs through knowledge and collaboration with other high influence functions.
Consider the top ten functions with the highest influence on product costs. How often, and how well do they collaborate to optimize product cost? The answer has much to do with their primary responsibilities.
A product engineer’s primary responsibility may be a design that will meet the product requirements and specifications, and which is released on schedule. A manufacturing / process engineer’s primary responsibility may be a manufacturing process and equipment which is safe and reliable. A manufacturing plant management teams’ responsibility may be to achieve daily delivery schedules with quality products. There is not much intersection of a focus on optimizing product cost. So why would there be a natural collaboration to optimize product cost?
Collaboration among the highest COGS influencing functions is necessary to achieve optimized product cost. No individual function has broad enough knowledge of the four key designs which drive COGS to effectively incorporate them alone. They need help from other functions. This is especially true when considering emerging developments and fringe knowledge within other functions’ scope. Take 3D printing as an example. It continues to evolve to deliver products that are bigger, stronger, and in less time. The manufacturing engineer should be highly familiar with the latest opportunities 3D printing offers. The product engineer may not be so familiar. So, their collaboration would enable a product design that can enable the use of the latest 3D printing opportunities to save COGS.
The collaboration of company employee functions to achieve optimized product cost won’t happen naturally. I have been told many times by leaders product development team functions, “We don’t need help to optimize costs. That’s part of our job.” To which I reply, “Then why do we have so many resources in place to remove millions of dollars in cost from our products that are in production?”
The collaboration around cost optimization needs leadership, expected goal achievement, resources, and management attention and support. These additions can elevate cost optimization to be among the primary responsibilities of the product engineer along with meeting requirements and the schedule. Likewise, all functions can have cost optimization elevated to being among their primary responsibilities.
In my book titled C-O-S-T, which stands for Cost Optimization System and Technique, I share how companies build the collaborative environment necessary to optimize their product costs during the product design and development phase. Doing so eliminates unneeded cost being passed into production and thereby maximizes product lifecycle profits.
|