31 Aug The Shortcomings (and Dangers) of Direct Labor-Based Costing at Manufacturers
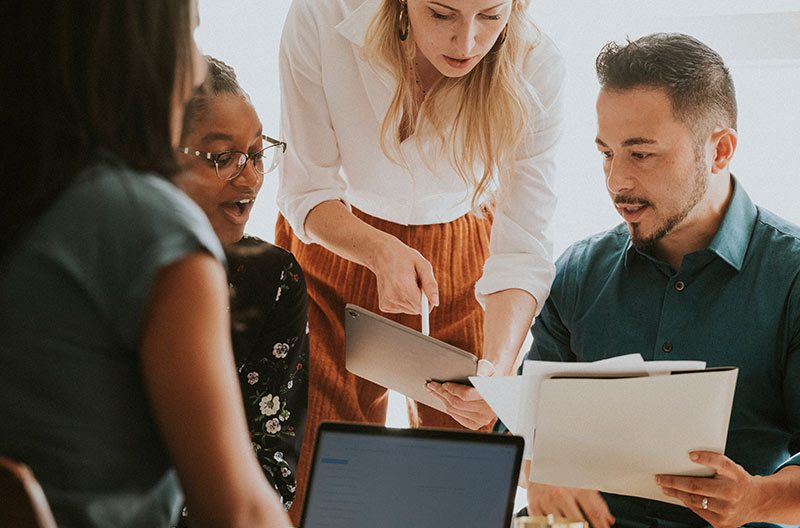
The Shortcomings (and Dangers) of
Direct Labor-Based Costing at Manufacturers
Douglas T. Hicks, CPA
Executive Summary
Direct labor-based costing models have retained their popularity among manufacturers in the 21st Century despite the major changes in both manufacturing technology and philosophy that have made them ineffective and their output misleading to decision makers.
Cost models driven by direct labor fail to take into account the true nature of the processes whose costs are being measured and whose rates being determined. Common areas of failure include: Cells and lines where each “focused factory’s” costs are unique and do not vary in proportion to the number of employees working in the cell or on the line,
In-process movement and storage whose costs cannot be linked to the appropriate products because they lie buried in direct labor-based rates and whose existence is made invisible to those seeking to improve operations and reduce costs,
CNC equipment, whose purpose is to both improve quality and reduce or eliminate direct labor, cannot have its cost accurately measured or assigned based on a resource it has been designed to eliminate.
The cost of acquiring and owning purchased materials, components and outside manufacturing services is also buried in direct labor-based rates – each purchased item’s “price” is treated as its “cost” – substantially distorting the true “cost” of purchases.
Post-manufacturing costs, most of which are not attributable to products, but to specific customers, are either ignored or incorporated in direct labor-based rates and spread arbitrarily among the company’s products
Continued use of direct labor-based cost models greatly diminishes the quality of a manufacturer’s decision making processes and, as a consequence, negatively impacts its bottom line. For example: Profitable business is lost and unprofitable business won because production costs have been inaccurately assigned to products, customer specific costs have not been assigned to customers at all, and other support costs have been arbitrarily spread over all products like peanut butter.
Lean and other process improvement initiatives are hamstrung as there is no cost data for most processes and those whose costs are measured are measured inaccurately.
Costly errors in insourcing, outsourcing and – most dramatically – offshoring products are made as a result of inaccurate and incomplete cost information.
The answer is not to implement a new, costly and complex cost accounting system. Instead, the answer is to develop and use a valid decision costing model that can be populated with data from existing sources to arrive at the accurate process, product, customer and incremental cost information necessary to support the high-quality business decisions required to survive and grow in an ever more competitive, worldwide marketplace.
Sorry, the comment form is closed at this time.